This article is one of a 16-part series on the fundamentals of stamping. Descriptions of all the articles in this series, and links to them, can be found at the end of this article.
Part XV of this series described several bending methods—wipe, coin, relief, pivot, and V. It also discussed springback and how to compensate for it when using these methods. This article focuses on other bending processes. Keep in mind that the key to success is to design the bending process so that it can be easily, quickly, and safely adjusted to allow for material variables.
Rotary Bending
Rotary bending perhaps is one of the most popular and effective ways of creating a precision bend. Rotary benders, also know commercially as Ready Benders® or Accu-Bend™ benders, have many advantages over conventional wipe bending methods. First, let's examine how they work.
Rotary or rocker benders consist of a foundation block, often referred to as the saddle. The saddle has a spring-loaded V-shape component called the rocker. This rocker rotates about its centerline and performs the bending action. It acts as both a holding pad and the bending mechanism.
Although this type of bender can be installed in almost any direction with respect to the ram travel, it most commonly is fastened to the upper die shoe. As the bender moves down, the rocker makes contact with the sheet metal. One contact point acts as a holding pad, while the opposite contact point rotates, creating the bending action. After the bend is completed and on the press's return stroke, the spring forces the rocker to return back to its original or idle position (Figure 1).

Figure 1
Advantages. Rotary bending has some advantages over other methods. The most advantageous feature is the simplicity of adjustment. Changes in the bend angle can be made simply by shimming or grinding the height of the assembly. Doing so takes very little time, and time is money.
Rotary benders can bend as much as 120 degrees and are well-suited to bending high-strength material. One company in Sweden has successfully created two 90-degree return bends in steel with yield strength of 980 mega pascals. This translates into steel that by U.S. standards has a yield strength of more than 142,000 pounds per square inch (PSI)—five times stronger than low-carbon steel. Attempting to make such a bend in a conventional wipe-bending operation most certainly would be impossible.
Another advantage is that, unlike conventional wipe bending, rotary benders require much lower forces to create the bend. Anywhere from a 40 percent to 80 percent reduction in force can be expected. This makes this method ideal for producing long, heavy-gauge, large parts, such as truck and semi frame rails.
You can expect less hole distortion in rotary bending. Consider a hole that is pierced in a flat blank and later bent into a vertical wall. During conventional bending, this hole can be subjected to a great deal of tension, which causes the hole to distort. Because rocker benders fold the metal around the punch, hole distortion is eliminated (Figure 2).

Figure 2
Inserting rockers with a special hard plastic called Delrin® can make them nonmarking, which is desirable when bending cosmetic-quality stainless steel or prepainted materials.
Rotary benders can used to bend up or down. They also can be placed on cam slides.
Disadvantages. Despite the many advantages, rotary benders do have some disadvantages. First, they can be quite expensive; however, consider the advantages of the reduction in downtime and frustration. Overall, they often pay for themselves in a short period of time.
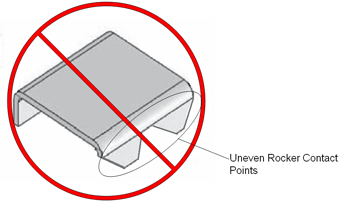
Figure 3
Poor Candidate for Rotary Bending
Also consider that you most likely will not need an external pad, which reduces die cost. Often the true cost of designing and building a conventional wipe bending die is much greater than the rocker bender. Don't confuse cost with value. In my opinion, rotary benders are worth every penny.
Because these benders have moving parts, there is a risk of galling up and failing to rotate. This can be prevented by periodicallycleaning and lubricating them.
Remember that rotary benders can be used for straight-line bending only. Avoid using them to bend special-shaped trim lines that do not allow for simultaneous punch contact. Angled corners are not good candidates for rocker benders (Figure 3).
Overall, I highly recommend using rotary benders for appropriate applications. They are available commercially from a few reputable suppliers.
Reverse U Bending
Reverse U bending is a unique but effective way of obtaining either a 90-degree bend or a bend with a slight negative angle. This process utilizes a high-pressure pad with an insert that can be adjusted in height by shimming or grinding it. The insert causes the part to bow upward in the center of the punch where a void has been created. Raising or lowering the insert changes the severity of the bow. Keep in mind that this bow must be created with the pressure exerted by the pad. This often requires the use of high-pressure gas springs.
After the bow has been created, the pad moves downward and the bends are established. Upon punch removal, the part has a tendency to spring back in the center, which causes the bends to "toe in." This method works well with materials that exhibit a great deal of springback. If the metal permanently deforms in the center bowed area, it may be necessary to push the part back flat in order to achieve a 90-degree angle (Figure 4).

Figure 4
Reverse U Bending Process
Remember that the true key to bending success is to design the tool in such a fashion that it can be quickly, safely, and accurately adjusted with respect to ever-changing incoming variables. Avoid using the grinding and welding process whenever possible.
Tidak ada komentar:
Posting Komentar